A lot of construction happened since the last blog post and we have moved into our (mostly) finished house. It is proving to be a very comfortable home and we can hardly wait for winter to see how it performs in the cold. Okay, maybe we can wait a bit for that.
Earlier we explored the foundation system and in this post we’ll discuss the wall and roof systems. Let’s quickly review the four basic control layers to be considered in every building enclosure:
1. Water: Keeps bulk-water out of the structure.
2. Air: Keeps conditioned air inside and unconditioned air outside. Air also holds moisture, so air moving through the structure is a bad thing. As the saying goes, build tight and ventilate right.
3. Vapor: Controls the amount of vapor permeance through the structure. It’s inevitable that some amount of moisture will get into your walls, so you need to allow them to dry-out.
4. Thermal: AKA insulation… Slows the transfer of heat through the structure.
The wall we constructed is a ventilated rainscreen system. A rainscreen is an exterior wall construction where the siding stands off from the weather barrier creating a capillary break allowing for drainage and evaporation. Some of the benefits of this system include prolonged life of the siding and finish (due to temperature and moisture equalization of the material), minimizing the chance of water intrusion into the wall structure, and keeping the weather barrier dry, thereby prolonging its life. To minimize the penetrations through the weather barrier the wall construction was sequenced in this manner: layout studs on floor deck, fasten plywood sheathing to face of wall, place rigid foam board over plywood (only tack in place), roll out building wrap over rigid foam board (do not fasten), place 1x3 furring strips over building wrap (located over each stud), fasten furring strips tight using 4” screws. The furring strips are what hold the building wrap and the insulation board in place. Below is a list of how the 4 control layers were handled:
Water: The metal roofing and underlayment keeps bulk water out of the roof system. The cedar siding is a rainscreen, keeping the bulk water out of the structure. Behind the siding the 3/4" air gap and building wrap act as the drainage plane for any water that makes its way through.
Air: Although great care was taken to control air intrusion at the exterior of the structure by using flashing tapes and minimizing penetrations, the primary air control layer is the gypsum board on the walls and the underside of the roof truss (see red line on diagram). The gypsum board was sealed to the wood structure to prevent air movement from the conditioned spaces into the wall and attic cavities. We used an EPDM gasket that was easy to install and provides an excellent life-long seal. We also used a similar gasket at the wall sill plates to seal the inconsistencies in the wood construction between wall and floor. All rim joists at floor to wall junctures were sealed with spray foam as this is a notorious air-leaking point.
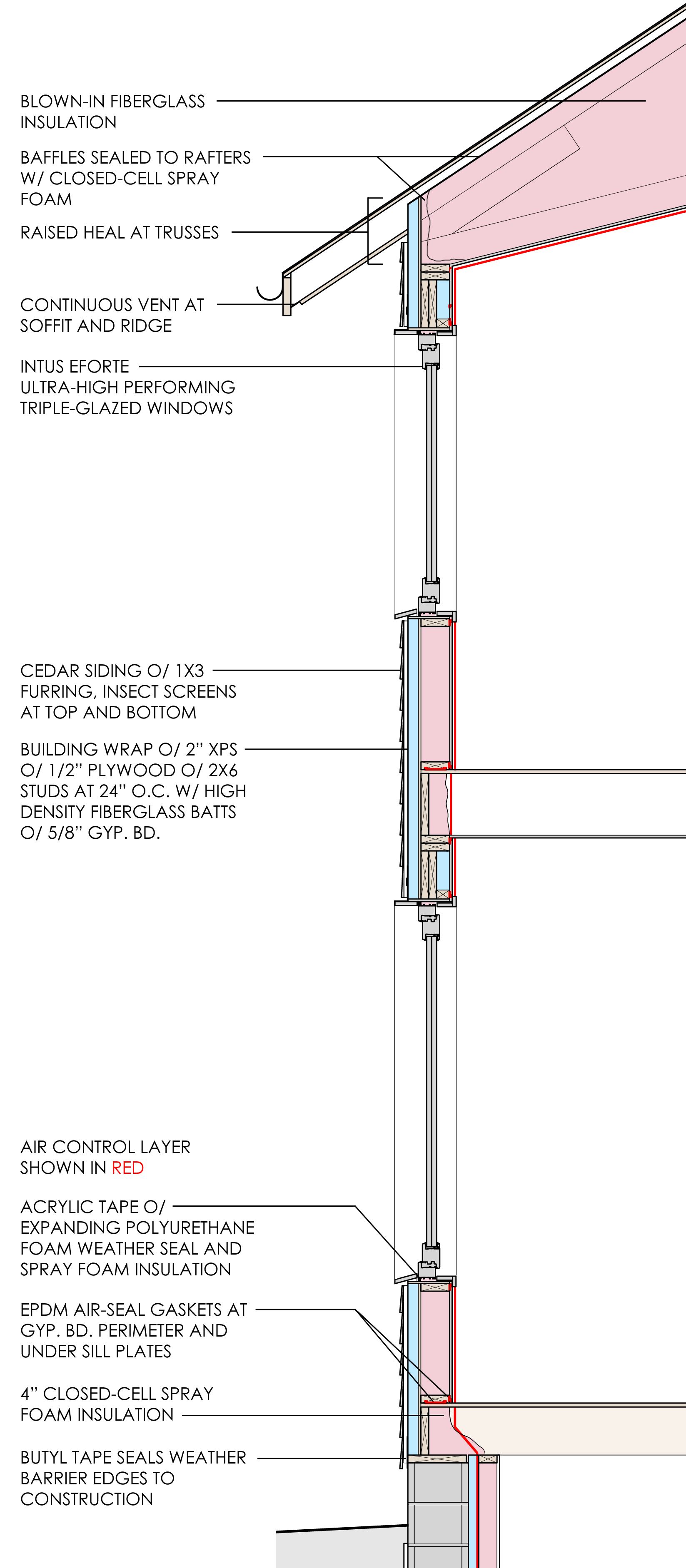
Wall Section Diagram
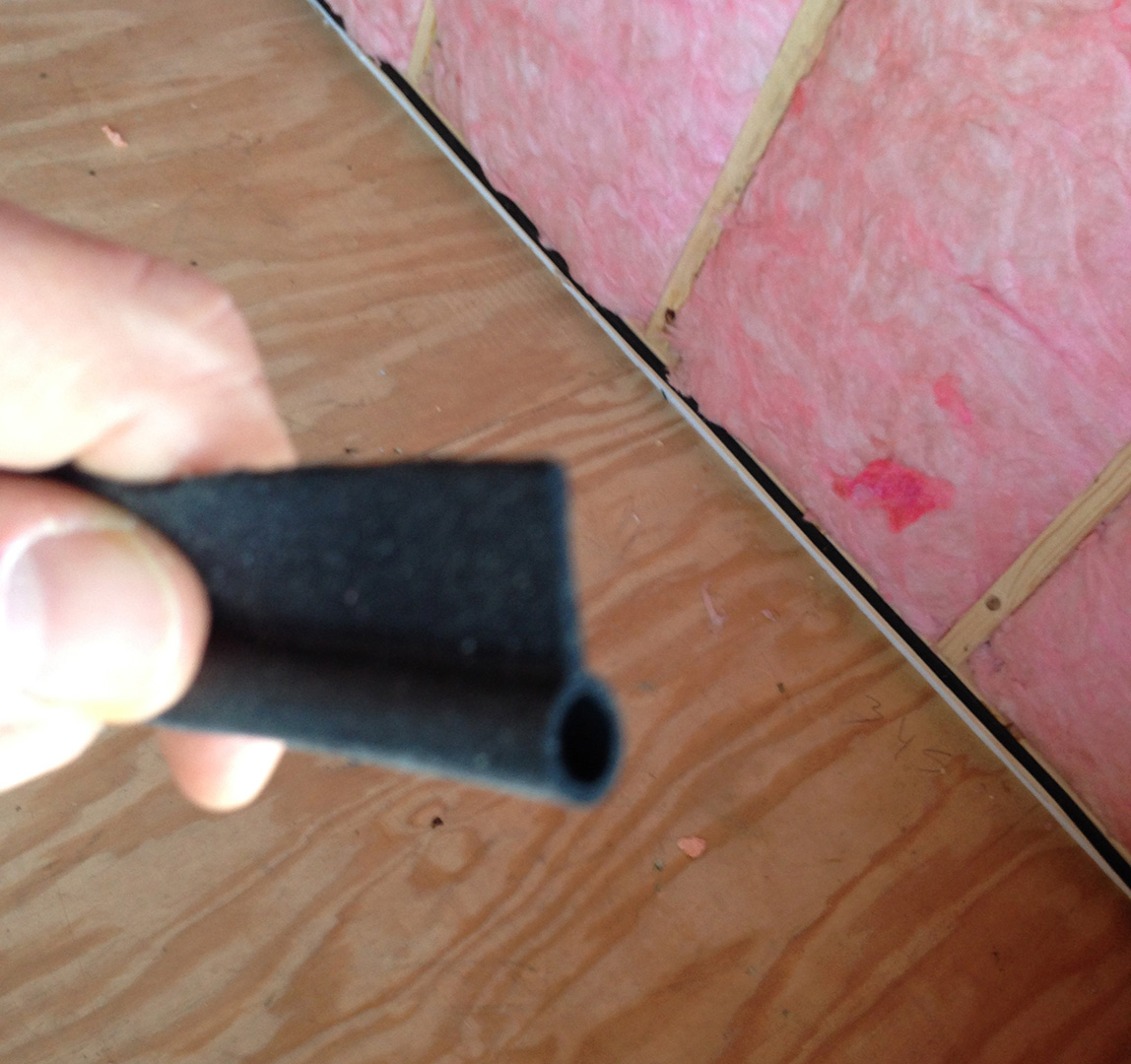
EPDM Gasket
Vapor: The vapor retarder employed is latex paint over 5/8” gypsum at exterior walls and the 2nd floor ceiling. It’s inevitable that some moisture will make its way into the wall system, so allowing the structure to dry back to the inside is important. Latex paint creates a vapor retarder, not a vapor barrier which would not allow the structure to dry. The attic is continuously ventilated at the eaves as well as the ridge which keeps moisture from building up within the roof structure.
Thermal: The structure of the wall is 2x6 wood studs at 24” o.c. and the cavities are filled with high density fiberglass batts (R-21). To enhance the thermal performance the exterior walls have 2” of XPS (R-10) continuous rigid insulation board. This continuity of insulation eliminates the effects of thermal bridging at the studs, resulting in a very high performing wall system. The attic is filled with blown-in fiberglass at an R-value of 100. The trusses were designed with a raised heal to allow for more insulation at the typical eave pinch-point. Care was taken to seal the baffles to the structure so air from the eave vents would not move through the insulation, stripping it of its thermal performance. The continuous eave and ridge vents keep the attic from becoming super-heated in the summer and keep it cool in the winter which prevents icicles from forming.
Combined with the foundation systems previously discussed and the Intus Eforte ultra-high performing triple-glazed windows, the building shell of the Modern Farmhouse should prove to drastically minimize the amount of energy needed for heating and cooling, all while keeping our family very comfortable.